SECONDARY
CONTAINMENT &
SPILL PREVENTION
Handling industrial chemicals comes with serious responsibility. A spill of hazardous materials can lead to environmental damage and costly cleanups, and it also puts on-site personnel in immediate danger. That’s why having a reliable secondary containment system in place is not optional, functionally and regulatorily speaking. Secondary containment is the safety net that catches potential spills if your primary storage fails, thereby preventing disasters before they can happen, or even in the midst of them happening!
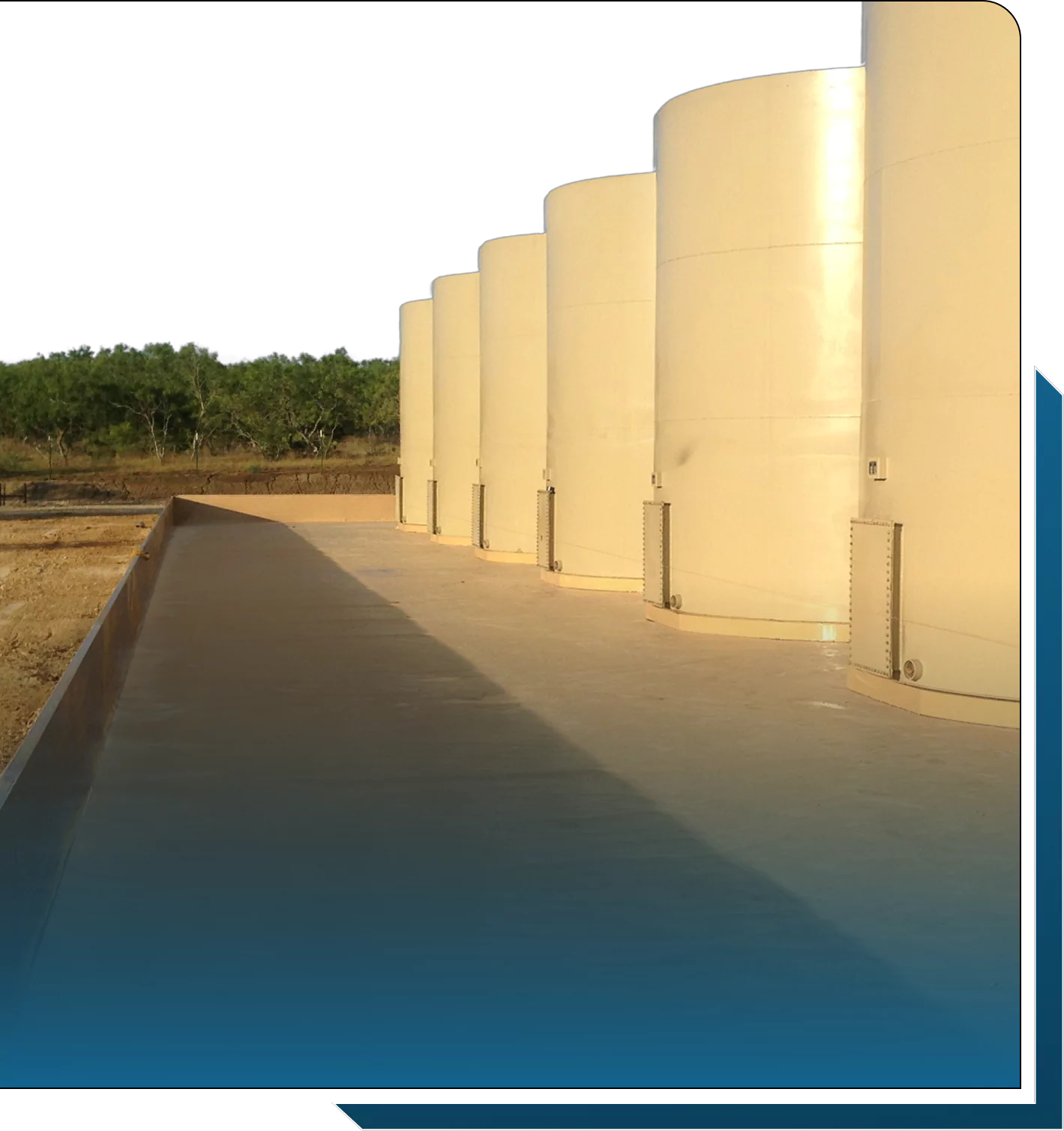
WHAT EXACTLY IS
SECONDARY CONTAINMENT?
Secondary containment refers to any system or structure that’s designed to capture hazardous liquids or other types of dangerous substances that escape from a primary containment unit (like a tank, drum, or other storage container). You can think of it as a backup barrier; if the primary container leaks or ruptures, the secondary containment structure (for example, a coated concrete spill berm or a lined pit) will hold the spill. This two-layer approach all but guarantees that hazardous substances and pollutants do not spread into the soil or into groundwater beyond the facility’s grounds. The primary container is the first line of defense (the vessel holding the liquid), and the secondary containment system is the second line of defense (a safety backup that keeps any leak within a controlled area). What exactly that secondary containment looks like is a matter of circumstance. Secondary containment systems come in various different types and sizes — from small benchtop spill trays and drip pans to large dikes and bermed containment areas surrounding storage tanks. But regardless of the form, the goal is the same, which is to provide sufficient capacity and a secure barrier to control potential spills.
WHEN IS SECONDARY CONTAINMENT NEEDED?
Secondary containment measures should always be in place whenever there’s a risk of a hazardous leak or spill that could harm the environment or people, no matter how large or small that risk. Many industries handling chemicals, fuels, or hazardous waste are actually required to have secondary containment by law, but it’s not just about compliance — secondary containment is critical for protecting the environment and human health, and that always takes priority number one. No two containment strategies are the same; however, while they don’t repeat, they often do rhyme, so here are a few representative scenarios where secondary containment is of vital importance:
Bulk storage containers at oil and gas sites must have secondary containment to prevent any oil spill from spreading. The EPA requires containment at these facilities under its spill prevention regulations.
Facilities storing chemicals or hazardous waste in drums or totes set up secondary containment in their drum storage areas. They might use spill containment pallets, curbing, or lined concrete pads to catch leaks from any drum and prevent contamination.
Even small-scale operations need secondary containment. Labs and workshops often use simple spill trays or basins under containers of hazardous substances. This provides immediate spill control if a bottle or container leaks, protecting surfaces and drains from exposure.
These examples represent only a few of the many different application areas of secondary containment. Anywhere—and we mean anywhere - where hazardous chemicals are used, transported, or stored, It is important if not required to provide workers and local environments with the protection that they deserve.
During fuel or chemical transfers, portable spill containment berms or drip pans can be placed under trucks and hoses. These mobile containment measures see that any leak or hose failure during loading is captured on the spot, without issue.
ARMORTHANE'S POLYUREA
SECONDARY CONTAINMENT TECHNOLOGY
ArmorThane specializes in polyurea and polyurethane coatings that turn ordinary containment areas into robust, leak-proof spill containment systems. Instead of relying solely on concrete or prefabricated liners, we apply our advanced sprayed-on coatings to create a seamless protective membrane that offers numerous advantages for secondary containment applications:
HIGH CHEMICAL RESISTANCE
ArmorThane’s coatings have exceptional resistance to corrosive chemicals, fuels, and solvents. They can safely contain a wide range of hazardous substances — from acids and oil to flammable liquids — without degrading or leaking.
SEAMLESS, CUSTOM-FIT LINERS
Our spray-applied polyurea/polyurethane forms a joint-free liner that adheres to every contour of the containment area. With no seams or gaps (even around pipes or drains) there are no weak points for leaks to escape.
ULTIMATE DURABILITY IN HARSH CONDITIONS
Our polyurea formulations cure quickly into a tough, rubber-like layer that won’t crack or peel. They withstand heavy use and extreme temperatures without damage, which is durability that ensures your containment remains reliable over time.
We bring not only top-quality products but also expert service. Our trained technicians can apply coatings on-site to new or existing containment units with minimal downtime. We take pride in engineering spill containment solutions that meet or exceed secondary containment requirements, tailoring each project to its unique challenges. The final result is a secondary containment system that is easier to maintain, fully compliant, and built to last.
SECONDARY CONTAINMENT REQUIREMENTS & REGULATIONS
Secondary containment requirements are set by agencies like the U.S. Environmental Protection Agency to ensure that spills are properly controlled. Regulations such as the EPA’s Spill Prevention (SPCC) rule for oil and RCRA standards for hazardous waste storage specify when secondary containment is mandatory to prevent the release of hazardous waste or other substances into the environment. Specifics vary by industry and material, but the key aspects include:
- CONTAINMENT CAPACITY: Secondary containment must have enough capacity to hold a major spill. A common standard is to contain at least 10% of the total volume of all primary containers, or 100% of the volume of the largest primary storage container, whichever is greater. This ensures that even if the biggest tank or vessel completely fails, the spill will be captured within the secondary containment structure.
- INTEGRITY AND IMPERMEABILITY: The containment structure should be built from materials with sufficient strength and chemical compatibility to resist leaks. It needs to withstand direct physical contact with the stored liquid and remain intact under harsh climatic conditions (extreme weather such as heavy rain or temperature swings). In practice, that means using an impervious barrier that provides strong chemical resistance — for example, a concrete berm coated with a compatible liner — so the liquid cannot penetrate or escape. In addition, facilities are usually required to perform regular visual inspection and maintenance of their secondary containment systems. Inspections help catch any cracks, erosion, or collected liquid so they can be fixed or removed promptly. Adhering to these requirements lets companies protect the environment and avoid costly fines, all while keeping workers and the surrounding community safe.
FREQUENTLY ASKED QUESTIONS
Primary containment refers to the main vessel or container that directly holds a hazardous liquid or material (for example, a storage drum or chemical tank). Secondary containment is the extra precaution — a structure or system like a berm, tray, or coated concrete basin — that catches the contents if the primary container leaks or fails. The secondary containment acts as a safety backup to prevent any escaped material from causing harm.
The storage and transport of most hazardous materials require the use of secondary containment strategies, which can include strong acids and bases, oxidizers, explosive materials, or anything else deemed a risk to human or environmental health and safety.
There is no single best type of secondary containment. Secondary containment strategies depend on the hazardous materials, the tools and equipment used for their transportation and storage, and the spaces that they occupy. Some technologies like polyurea offer a more flexible solution that can be used in most applications, while others such as spill pallets or decks offer narrower function.
In the United States, environmental laws make secondary containment mandatory in many situations involving hazardous liquids. The EPA’s Spill Prevention (SPCC) rule requires containment for large oil tanks, and RCRA regulations cover hazardous waste storage areas. Most often, if you store significant volumes of oil, fuel, chemicals, or hazardous waste, you are required to have a secondary containment system.
ArmorThane’s spray-applied coatings create a seamless, leak-proof liner inside your containment area. The extra layer this provides covers any cracks and imparts superior chemical resistance, so hazardous liquids can’t seep through. The coating also reinforces the structure, allowing it to withstand heavy use and temperature changes without cracking. It turns a standard containment area into a much more durable and reliable spill barrier.
Absolutely. One major advantage of our coatings is that they can be applied to existing structures. Your old containment (whether concrete or steel (even stainless steel)) can be cleaned and prepped and then the coating is sprayed on. It bonds to the surface and quickly forms a new seamless liner, sealing any cracks. After curing, your aged containment area has a fresh, leak-proof lining — a fast and cost-effective upgrade compared to building a new containment system.
PROTECT YOUR WORLD AGAINST SPILLS
WITH ARMORTHANE
‘Good enough’ is nowhere near enough when it comes to spill protection. ArmorThane delivers proven secondary containment solutions that give you confidence, not to mention regulatory compliance. Whether you need to line a new berm or repair an aging containment area, our team is ready to help. Contact us today to discuss your project and learn how our polyurea and polyurethane coatings can safeguard your operations from spills. Protect Your World with ArmorThane — we’ve got you covered; literally.
ABOUT THE AUTHOR
TYLER GLECKLER
CONTACT US
REQUEST A QUOTE
ArmorThane has built a strong reputation over the past 30 years for producing high-quality, durable protective coatings.
Phone Number
Tel: 417.831.5090
Email Us
moreinfo@armorthane.com