TO SPRAY OR NOT: HOW WEATHER CONDITIONS CAN MAKE OR BREAK YOUR PROTECTIVE COATING APPLICATION
Protective coatings have become part and parcel of modern private, commercial, and industrial applications. Whether they’re used for your home’s crawl space, your business’s tools and equipment, or even your city’s water treatment infrastructure, protective coatings can be widely employed for added protection and myriad other benefits. However, there’s both an art and a science to applying spray on coatings, requiring extensive training and certification, and likely several years in the field, before being able to truly master the craft. Among the many tips and tricks, rules and best practices, is an understanding of how weather, and other local environmental conditions, can impact the application process. So today, we’ll review how protective coatings are applied, explore the key weather conditions to consider, and learn how to navigate them for a high-quality coatings system in any environment.
HOW TO APPLY PROTECTIVE COATINGS
Before we talk about how weather can affect applications, we should start by talking about how spray on coatings are applied in the first place! While the application process will vary depending on the type of Protective coatings, there are generally three main steps:
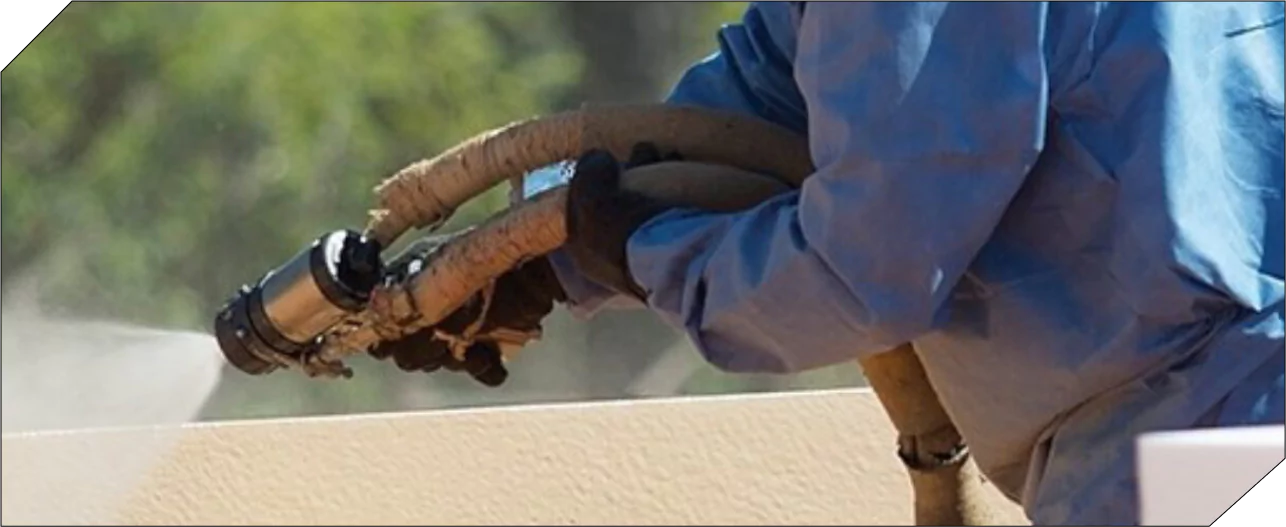
01
SUBSTRATE PREPARATION
The substrate is the surface being coated, and its preparation represents the first, and perhaps the most challenging part of the application process. To prepare the substrate, it must be thoroughly cleaned, removing any and all contaminants that may obstruct adhesion between the coatings and the surface of the substrate. This may include grease, oil, dust, or other debris, so this cleaning step will follow any repairs for applications of new coatings on old surfaces. In some cases, more aggressive preparation may be required, which can include grinding, sandblasting, or priming, among other surface treatments. The specific substrate preparation procedure will depend on the type of substrate, the coatings formulation, and the environment and function of the coatings system.
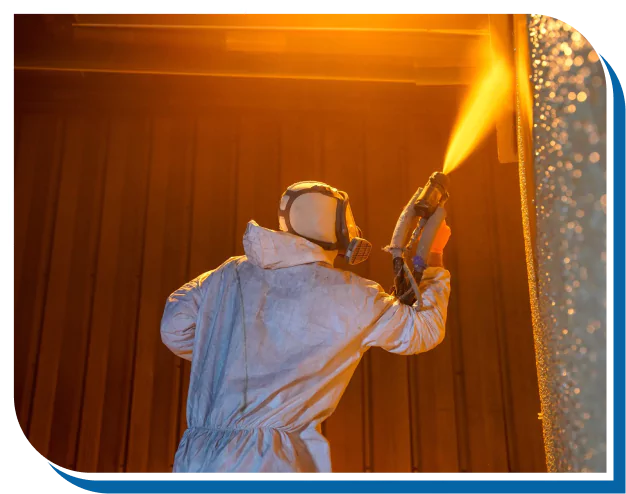
02
SPRAY ON APPLICATION
With the substrate prepared, it’s time for application using innovative high-pressure spray equipment. Layer by layer, applicators wield their equipment to create a seamless, uniform membrane that separates the substrate from its local environment, protecting it for years to come. As we’ve already said, there’s both an art and a science to spray on applications, and we offer a comprehensive training program and all the tools you’ll need to become a professional applicator and start your own coatings business.
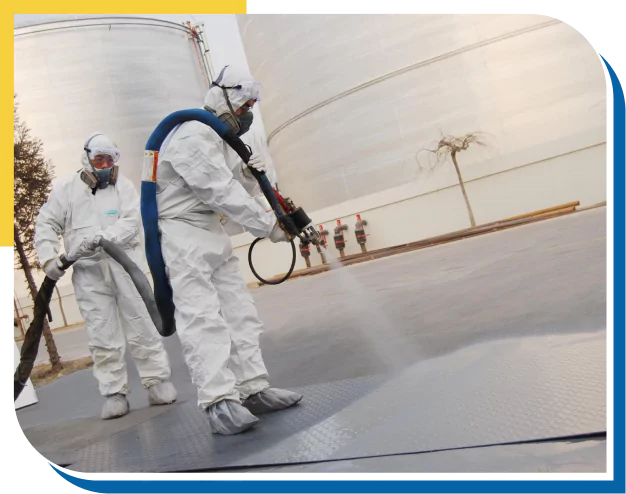
03 DRYING AND CURING
The last step, following the application, is to step away from the installation and allow time for everything to dry and cure. This happens at an incredible rate for advanced coatings like polyurea, curing within minutes to see a user-ready surface the same half of the day as the application. Other technologies, like polyurea’s sister material polyurethane, are slower to cure, but remain far quicker than many alternative technologies, curing in as quickly as a few hours under optimal conditions.
And that’s it! While straightforward, and easy for professional applicators, the devil is in the details; executing each of these steps requires expert training and certification, and a comprehensive knowledge about the materials, equipment, and application best practices. This includes a robust knowledge of how weather conditions can influence applications, which is often overlooked, if not unknown, even to some experienced applicators with more than a few layers under their belt.
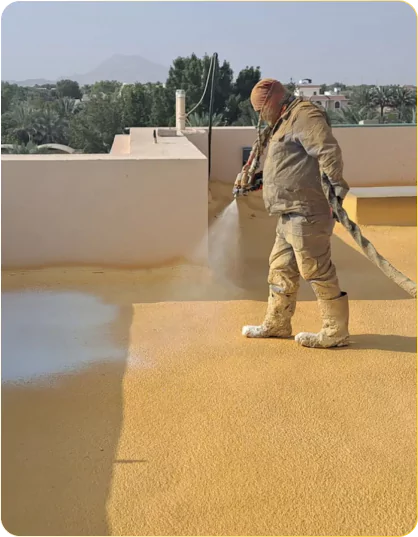
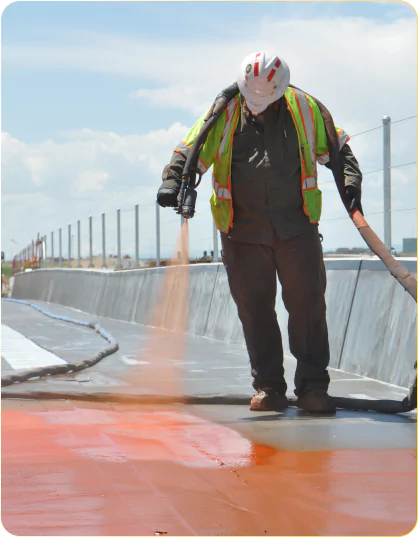
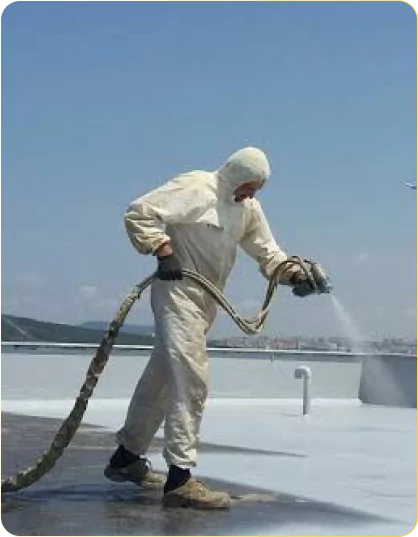
4 KEY WEATHER CONDITIONS TO CONSIDER
WHEN APPLYING PROTECTIVE COATINGS
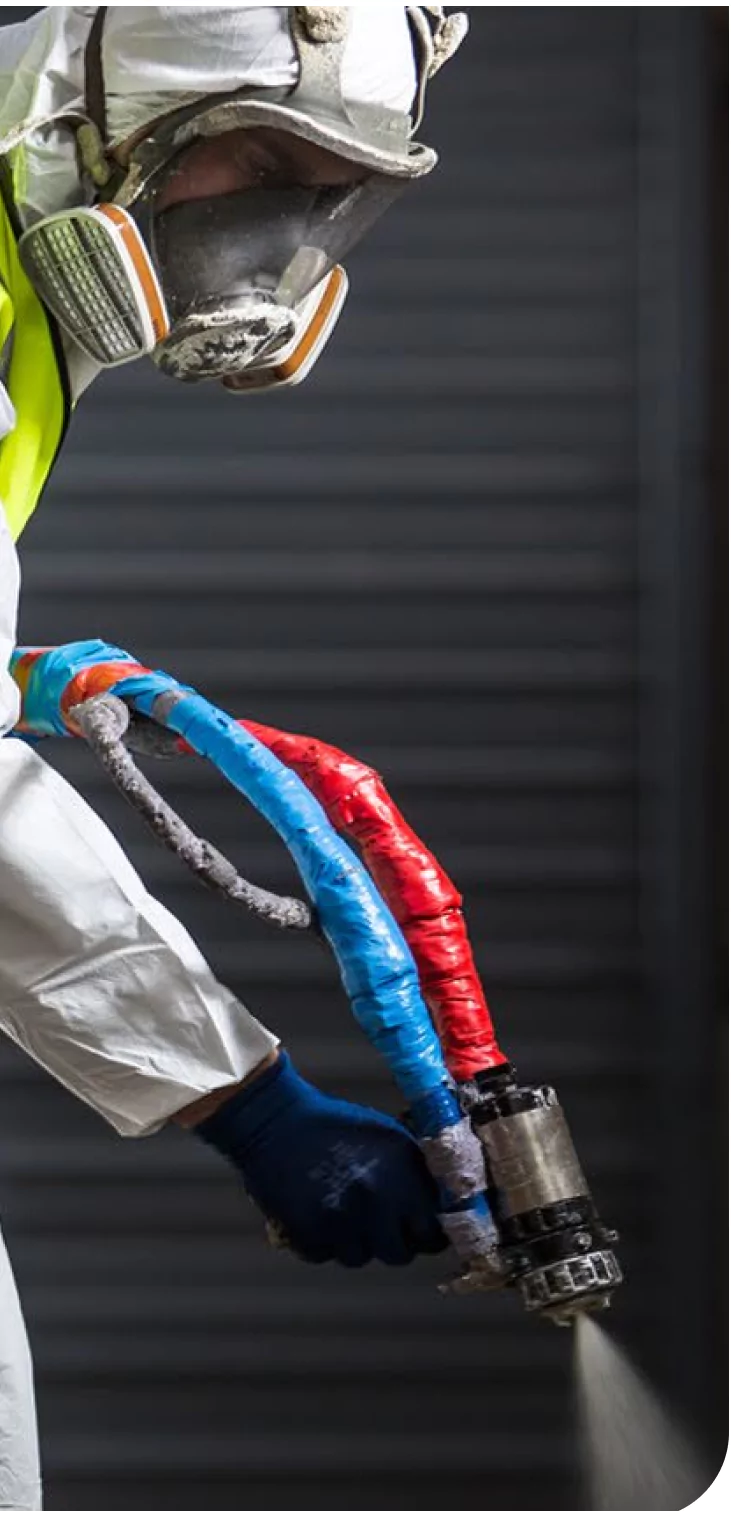
TEMPERATURE
Temperature is the first, most obvious, and arguably, the most important weather condition to consider when applying spray on protective coatings. However, there isn’t just one temperature to monitor and account for; several different temperatures play a major role in the quality of application, including the ambient temperature, substrate temperature, and dew point temperature.
AMBIENT TEMPERATURE
SUBSTRATE TEMPERATURE
The substrate temperature, as you may have guessed, is simply the temperature of the substrate, or the surface to be coated with protective coatings. While it’s often true that the ambient temperature and the substrate temperature are the same, this isn’t necessarily so, and there can even be large disparities between the two temperatures. Precise monitoring of the substrate temperature is thus essential, as the substrate temperature must remain at least 5°F (3°C) above the dew point, which we discuss more in the next section. The point is, if the substrate temperature is too close to the dew point, moisture will condense on the substrate’s surface and impede the quality of adhesion.
DEW POINT TEMPERATURE
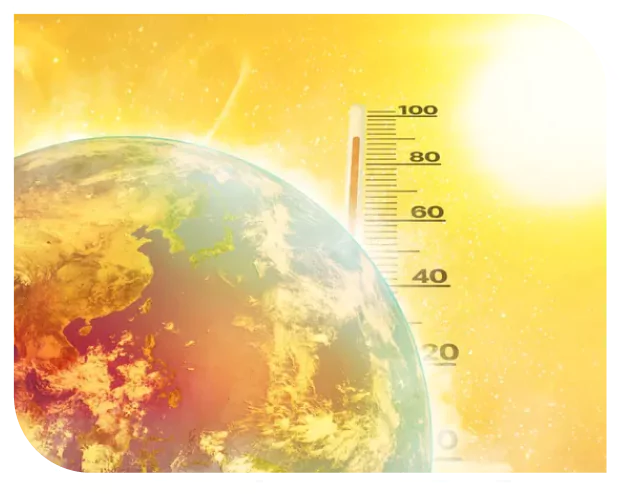
HUMIDITY
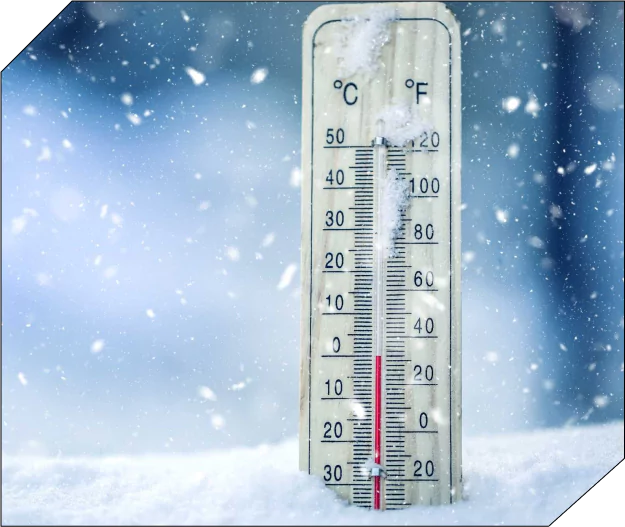
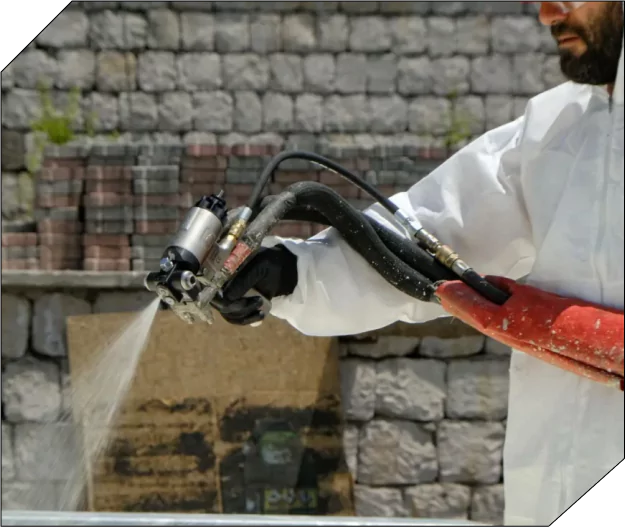
WIND SPEED
The role of wind speed in the application of protective coatings is likely more obvious than that of temperature or humidity; if wind speeds are high, then your installation risks being doped with dirt, dust, trash, plant material, or really any other nearby objects light enough to be carried by the wind. Moreover, the wind itself can also directly damage application quality, especially for the thicker, more voluminous polyurethane spray foam. After spraying layer by layer into a uniform membrane, strong gusts of wind risk taking what was straight as a level, and turning it into a slope fit for the skatepark.
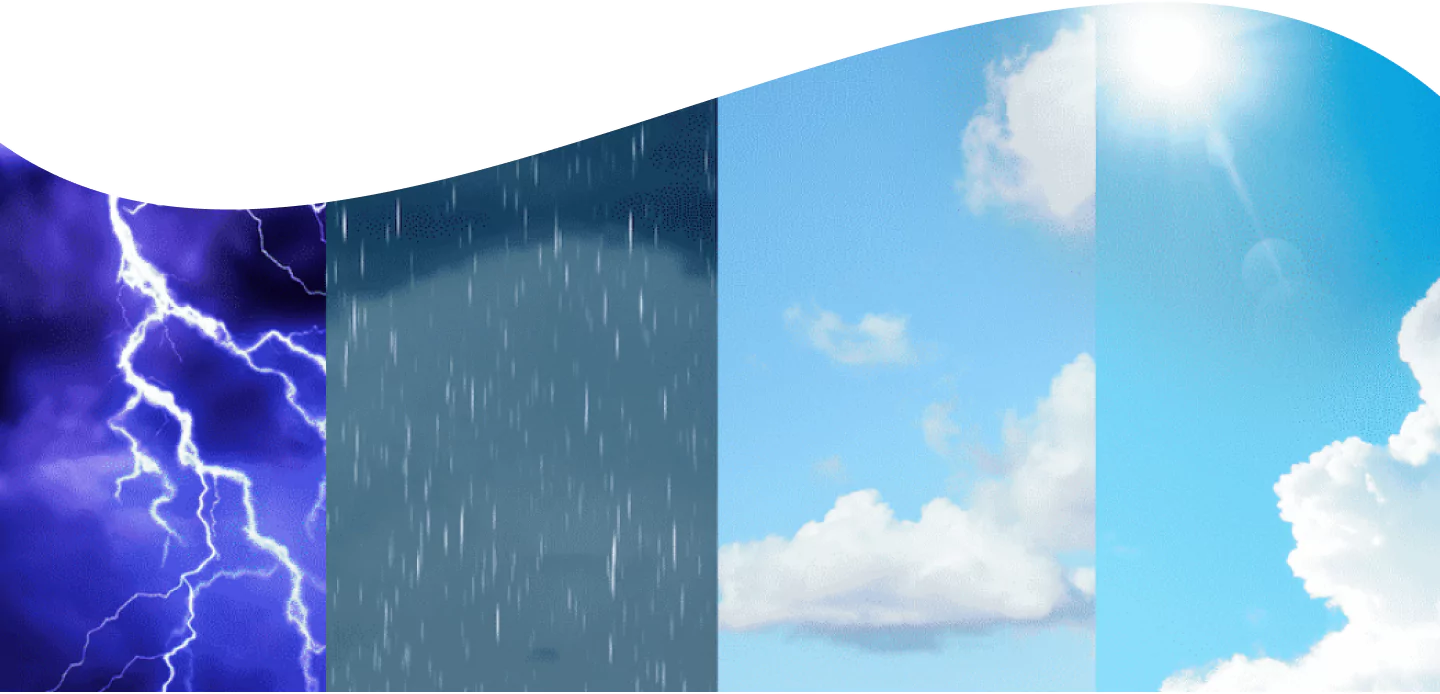
ALTITUDE
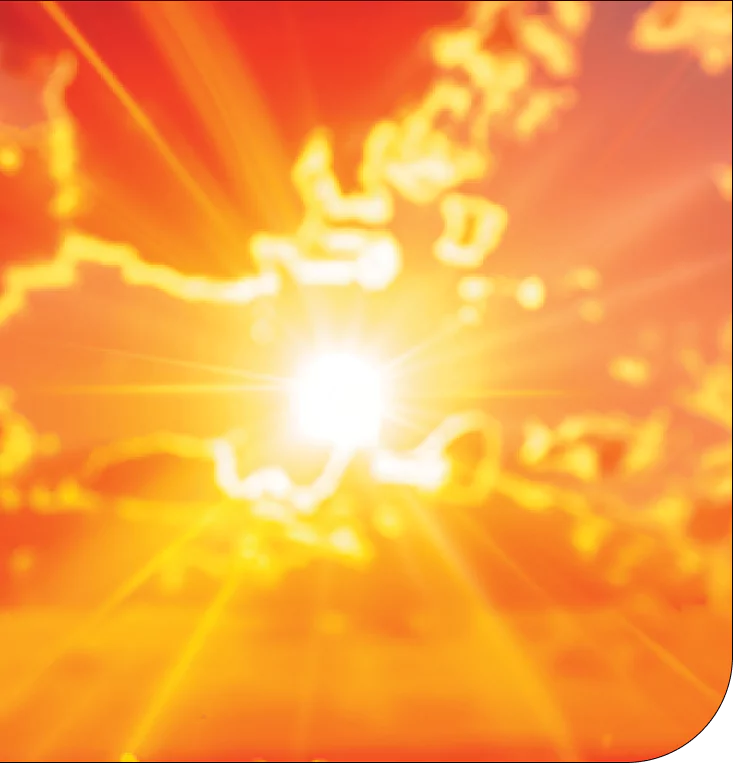
latest news & bLOGS
FAQ FREQUENTLY ASKED QUESTIONS
LEARN MORE ABOUT
HOW TO APPLY PROTECTIVE COATINGS
Today’s discussion is just the tip of the iceberg when it comes to learning all the tips and tricks to install high-quality protective coatings. If you’re interested in learning more, ArmorThane offers comprehensive startup packages with everything you need to master spray on applications and start your own coatings business. With only a small initial investment, and no franchise fees or other predatory profit-stealing practices, you’ll be off and ready to go, serving your own clients, on your own time, for your own profit. Our packages include personalized on-site training, high-quality materials, advanced high-pressure spray equipment, and lifetime technical support. So when we say comprehensive; we mean it! To learn more, contact us today! Our 24/7 teams of customer service and technical support staff are never more than a call away, ready to help with anything you need.
CONTACT US
REQUEST A QUOTE

Phone Number
Tel: 417.831.5090
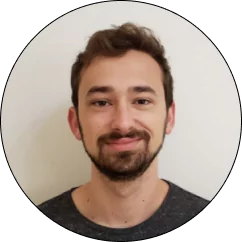